How to select a compressed air system services provider
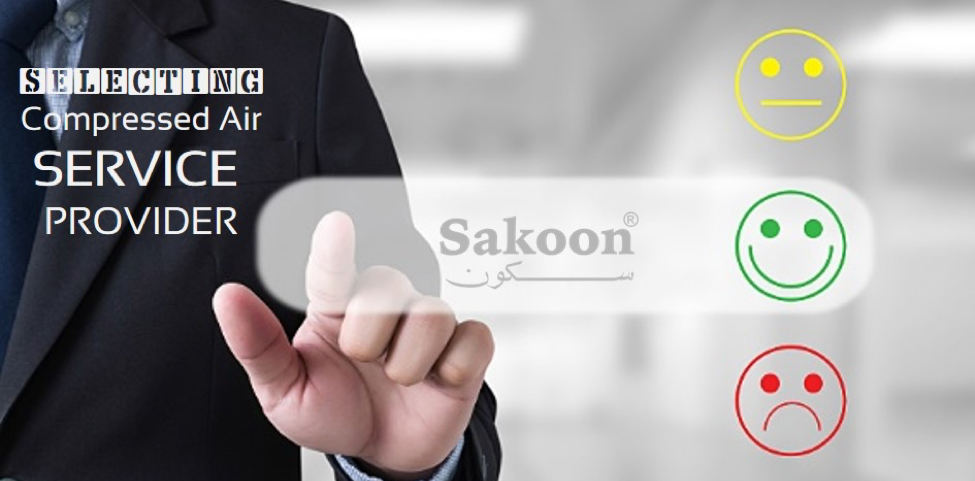
The biggest challenge any factory professional faces in Pakistan is finding the correct answer to the following question: “How do I know if the service provider I hired to evaluate compressed air systems has the necessary skills to do so?”
The production of compressed air is a dynamic system. Many factors affect its performance and reliability. Some of these factors may have nothing to do with the air compressor itself, or even with the compressor room. So the next time you are interested to contract a service provider, consider these set of guidelines to determine both the qualifications needed in a service provider and the scope of work level that will fit your needs best.
- Training
Ask the company to provide training documentation for their sales and service personnel. Technology advancements require constant training of any team dealing with compressed air systems. The company should share details of training institutes and certifications for every service engineer.
- Compressor knowledge and expertise
Does the service provider have the expertise to work on every compressor type in your facility? How much experience does the service technician have? How do they train? Do you participate in formal education? Knowledgeable service technicians deserve the high price they may need because they can troubleshoot and efficiently bring the device back online.
- Component controls knowledge and expertise
Handling, accessories and auxiliary equipment. Does the service provider have expertise in refrigeration and other work on dryers and related equipment? Is the service provider able to repair the type of filters, drains, distribution and point-of-use equipment in your facility?
System controls. Does the service provider have diagnostic and technical control functions to determine how to optimize the existing control configuration and suggest improvements? Can the service provider use the network compressor together or monitor it remotely as needed? Advanced controls can save energy and improve reliability by automatically starting and stopping, and turn off the compressor so that it can be used as a backup device. Early warning through remote monitoring can help you discover problems before they become serious downtime.
- Availability of compressed air system assessment services
Does the provider offer compressed air system analysis services? If yes, how well do they fit your needs? If no, can the provider outsource these services to an experienced system specialist? How experienced are the individuals who will be providing these services? Once a walk-through, assessment or audit is performed, what kind of follow-up services are available to ensure that recommendations are implemented properly and produce the desired results? Ask for client references, a sample of similar work that the provider has done for others and resumes of the personnel who will be performing the work. Please note that while leak detection is a useful element of a system assessment, a true system assessment includes much more.
- Company capabilities
Ask about the service provider’s standards of performance for:
- Annual Service Contract
- Emergency service response
- Air-end Refurbishment
- Parts shipments
- Compressed Air Health-check services
- Installation and Commissioning
- Emergency Rental Fleet
- Service facilities
Visit the facilities of two or three service providers under consideration to see first-hand the type of repair shop and parts warehouse with which you will be dealing.
Sakoon Pneumatics is an Authorized Service Provider for Both CompAir and Gardner Denver (Ingersoll Rand) Brand of Air Compressor and Associated Accessories in Pakistan.
We also provide Premium Screw Air Compressor Services and Spares for all types of other famous brands.
Experienced in Compressed Air Systems for 40 years, Sakoon Pneumatics is known for excellent services and after-sales support. Depending on Industrial needs, our team of qualified technicians schedule ideal maintenance plans for your compressed air system which lead to optimum machine performance, reduced downtime and increase productivity.
Leave a Reply
Want to join the discussion?Feel free to contribute!