Why Your Compressor System Needs Preventative Maintenance
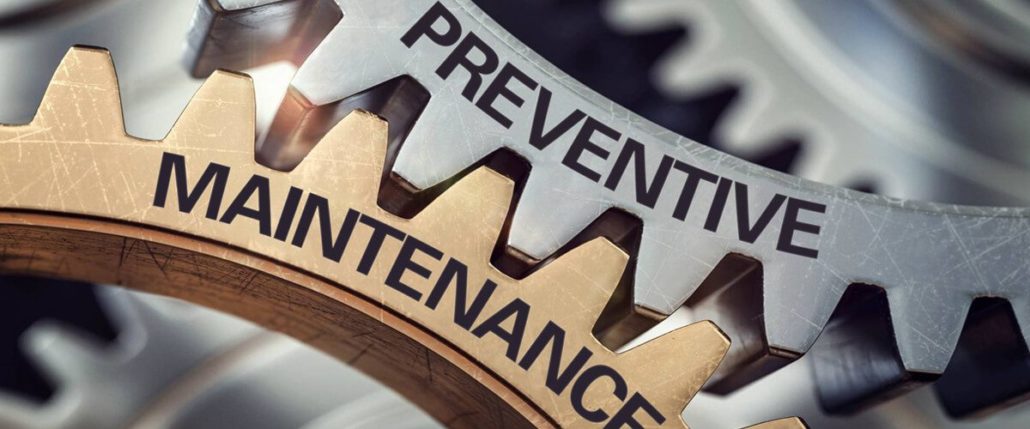
Air compressors are the workhorses of the industrial world, ensuring that production and application needs are met in facilities across the globe. However, compressors are only machines – they’re not infallible. This is what makes compressor system maintenance incredibly important! Instead of waiting around for a problem to pop up and reactively requesting service and repairs, why not proactively stay on top of your compressor’s maintenance needs? This is called preventative maintenance – i.e. preventing issues like clogged filters, broken belts, and burned out motors from arising before they have a chance to start.
Why Your Compressor System Needs Preventative Maintenance?
Uptime, efficiency, and reliable production are critical elements for every business. Preventative maintenance helps to ensure that your compressor system continues to function as it should, thus helping decrease the risk of shutdowns. Still not convinced? Compare it to routine car maintenance. To keep our vehicles in tip-top shape, we schedule regular visits at a dealership for oil changes, tire rotations, and filter replacements; this usually prevents larger car concerns from popping up down the road. The same concept applies to air compressors! The more effort you invest in keeping your compressor system in well-functioning condition, the better its operation – both now and in the future.
The Benefits of Preventative Maintenance
Proactively maintaining your air compressors comes with a variety of concrete benefits, no matter the size or shape of your operation. These benefits include:
Dodge That Downtime. A compressor that hasn’t been regularly serviced won’t be working at its best. Contamination such as oil leaks within the unit, oil that needs changing, or blocked filters could be preventing your compressor from performing as it should. The result? Higher energy bills, a greater carbon footprint, and a reduction in the lifespan of the machine. You’ll also put your compressor system at risk of experiencing performance issues more frequently.
Sidestep Unexpected Costs. Emergency repairs don’t come cheap! On top of service costs, you could easily be looking at thousands (if not tens or hundreds of thousands) of dollars in lost productivity or spoiled end-product. Depending on the severity of the problem, you may even have to replace your compressor system altogether; this also says nothing about the high energy bills caused by a compressor’s inefficient operation. Don’t risk taking this kind of hit to your bottom line!
Get Serious About Safety. It’s important to realize that your compressor doesn’t have to have a catastrophic failure to contribute to a poor or unsafe work environment. A poorly serviced compressor may be generating excessive heat and noise, and unseen or unidentified issues can lead to things like fire hazards, electrical shorts; it can even indirectly and cause other machines to malfunction. The last thing you want to do is discover an issue with your compressor system after it led to an employee injury.
Extend Life Expectancy. Air compressors are a significant investment, which means that extending the life and efficiency of this equipment should be at the top of your to-do list. Preventative maintenance helps you achieve this, ensuring that your compressor system will run smoothly for a long time.
Maintain Control Over the Maintenance Schedule. A perk of preventative maintenance is maintaining control over the maintenance schedule. Rather than having a compressor breakdown dictate the time for service, you get to choose when the service happens. Need to schedule it for a weekend, holiday, or after hours? Not a problem! Stay in control of your operations by including maintenance as something you plan for, rather than treating it as a disruption to your plans. The caveat here – make sure that you adhere to the suggested service schedule set forth in your equipment manual!
Routine Preventative Maintenance Tasks
Preventative maintenance differs for each compressor based on model, size, technology type, running hours, and installation environment. This means that the maintenance expected for a 5hp piston compressor in an auto body shop will vary from a 250hp oil-free rotary screw compressor in a pharmaceutical application! Your compressor manual will outline the specific maintenance tasks expected for your compressor. With that being said, checking the compressor filters, belts, bearings, vents, and oil levels (if an oil-injected machine) are all components that should be inspected regularly. Additional recommended preventative maintenance checks include:
Air Filters and Oil Separators. Air filters are essential to protecting your compressor system from dirt, debris, and other pollutants that would otherwise enter your compressor. Oil separators, on the other hand, help filter out oil from the compressed air before the air leaves the compressor (in oil-injected machines), thus keeping your compressed air clean. Both air filters and oil separators are critical to your compressor’s operation and must be checked, cleaned, and replaced at regular intervals.
Piping Contamination and Clogs. Compressed air piping installations are key in getting the compressed air to where it needs to go. You should check your piping system for any type of contaminants, including rust and dirt, to help prevent pressure drops.
Is That Condensation? Compressing air results in hot, wet air, which turns into condensate. As this condensate builds up within the compressor, it can lead to large issues, including poor air quality, process contamination, etc.
Compressor service contract and parts for “EVERY COMPRESSOR, EVERY BRAND” in Pakistan.
📞 +92 333 0135392 ; +92 334 5933391
📧 info@sakoon.com.pk
Leave a Reply
Want to join the discussion?Feel free to contribute!